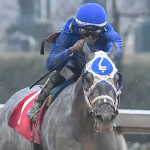
Preakness Quick Sheet: Get to Know the 2021 Preakness Horses
As the planet learns to deal with the COVID-19 pandemic, most are doing what they can to survive. Others are using creativity and innovation to help serve those in need.
The medical community — on the front line caring for those infected with the virus — is perhaps the most affected. Beyond the physical and emotional demands of their jobs, access to equipment and supplies is an ongoing struggle as state and local authorities scramble to keep pace.
Enter Adiclere Evans and Lexington-based Bloodline Products. The maker of jockey silks, among other Thoroughbred racing-related items, has shifted its resources to begin making two different types of surgical masks along with hospital gowns for doctors and nurses. Her team of seamstresses, from Del Mar, Calif., to Kentucky, to Snellville, Ga., are cranking out product “as fast as we can make them.”
Evans is the daughter of Adele Green and the granddaughter of Patricia Headley Green, who founded Silks Unlimited in the early 1990s. Green is the daughter of Hal Price Headley, one of the founders of the Keeneland Association. After Patricia Green passed away in March 2017, the company morphed into Bloodlines Products, an online store that also offers racing apparel and gifts. While Adele Green lives in Lexington, her daughter lives in Charleston, S.C.
Like everyone, Evans and her mother saw the rise of COVID-19 cases begin to mount in the U.S.
“We saw the wave coming for America and it took about a week for it to sink in and wrap my head around it,” Evans said. “Last week it hit me that, wow, we can make all of these products. We have to learn how to make hospital supplies.
“Our seamstresses are amazing, they went into overtime,” she said. “We were beginning to see a little stoppage in our business, so we thought, ‘What is the next step?’ They knew they needed to do something.
“We got the ball rolling by communicating with the (U.S. Food and Drug Administration) and the (Centers for Disease Control and Prevention), and we got patterns for the masks. We are currently doing two types of masks,” Evans said.
“One is the surgical mask that is pleated; the one you see the doctor’s wearing. And we do a filtered mask that is the equivalent to the N95 (a filtering system that removes 95% of 0.3+ micron particles). We can use two pieces of material and put one piece of approved filter between it and it is considered ‘N95 filtration.’ We can do up to 30,000 of those. We are trying to ramp up production of those.”
At present they can produce a total of 6,000-12,000 masks in a week.
“At first we wanted to just get going,” Evans said. “But there are costs. We created a Go Fund Me account to try and get some initial capital.”
Donations can be made by visiting the Go Fund Me page.
“We also are doing some gowns. We just got the pattern down, and we are trying to get the materials. Also, the plastic that goes in the brim of horse racing helmet covers, the vendor who provided the plastic for it, they are hopefully going to be able to start making face shields.”
It’s one thing to want to do right thing, but there’s more involved: providing the correct equipment, and then making sure, logistically, your product can be delivered.
“My sister is a lobbyist in Washington, D.C., and she sent me articles about the need for hospital supplies,” Evans said. “I contacted some senators and hospital groups and there is a national hospital group we just connected with that provides supplies to 2,500 hospitals and clinics. Their need is unlimited.
“I’m trying to bring our labor, suppliers, and vendors together and source through what we already have, and see who can do what. We need anybody who can sew on a massive scale ... that would be helpful,” Evans continued.
“It’s unfortunate because I’ve been talking with some people at hospitals that have had to throw away homemade masks because they are not approved by the FDA or made by CDC guidelines. That is why we did that. We have two senators helping us fast track the filtration masks so we could get approval. We applied for what is called an emergency use application. That will get them to look at our products and make sure they’re made with the correct specs and materials and get their approval. Then we can really ramp things up on a larger scale to the medical community.
“We are in a situation where we are making them and going as fast as we can,” Evans said.
As with Thoroughbreds, speed is paramount.